When optimizing your warehouse material handling, there are certain best practices worth considering. In this article, we will take a closer look at why the proper handling of warehouse materials is so important, how different tools, equipment, and technology can make such handling safer and more efficient, and how making changes, both large and small, to your warehouse operations can help you increase profits, boost productivity, keep your employees safe, and keep your customers happy.
Why warehouse material handling is so important
Proper handling of warehouse materials is important for a variety of reasons. Most notably, it can affect your warehouse’s productivity, safety, profitability, and customer satisfaction.
Productivity
By finding ways to streamline materials handling, your warehouse can hasten turnaround times. This reduces the resources spent on idle time in the warehouse and ensures that overall operations are as lean and efficient as possible.
Safety
Proper handling procedures, regular and thorough training, adherence to all rules and regulations, and the appropriate maintenance and use of warehouse equipment can drastically reduce the risk of warehouse accidents and injuries. Most importantly, these procedures keep your team safe. Adherence can also protect your operation from consequences that affect productivity and profitability, such as fines and shutdowns.
Profitability
As mentioned, both productivity and safety in warehouse materials handling can ultimately affect your operations’ profitability. But best practices can also be implemented to ensure your warehouse operation is operating as profitably as possible. This means implementing warehouse management and inventory management strategies that minimize waste, human error, and inventory shrinkage.
Customer satisfaction
Finally, every strategy implemented to optimize warehouse material handling will ultimately lead to efficiency that leaves your customers more satisfied than ever before. First and foremost, customers expect timely and accurate order fulfillment. Provide that, and you’ll already enjoy happier buyers and an improved reputation.
But, suppose you can get your operation to run even more leanly. In that case, you could offer volume pricing, even faster service, or some other high-value benefit that helps you stand out from the competition even better.
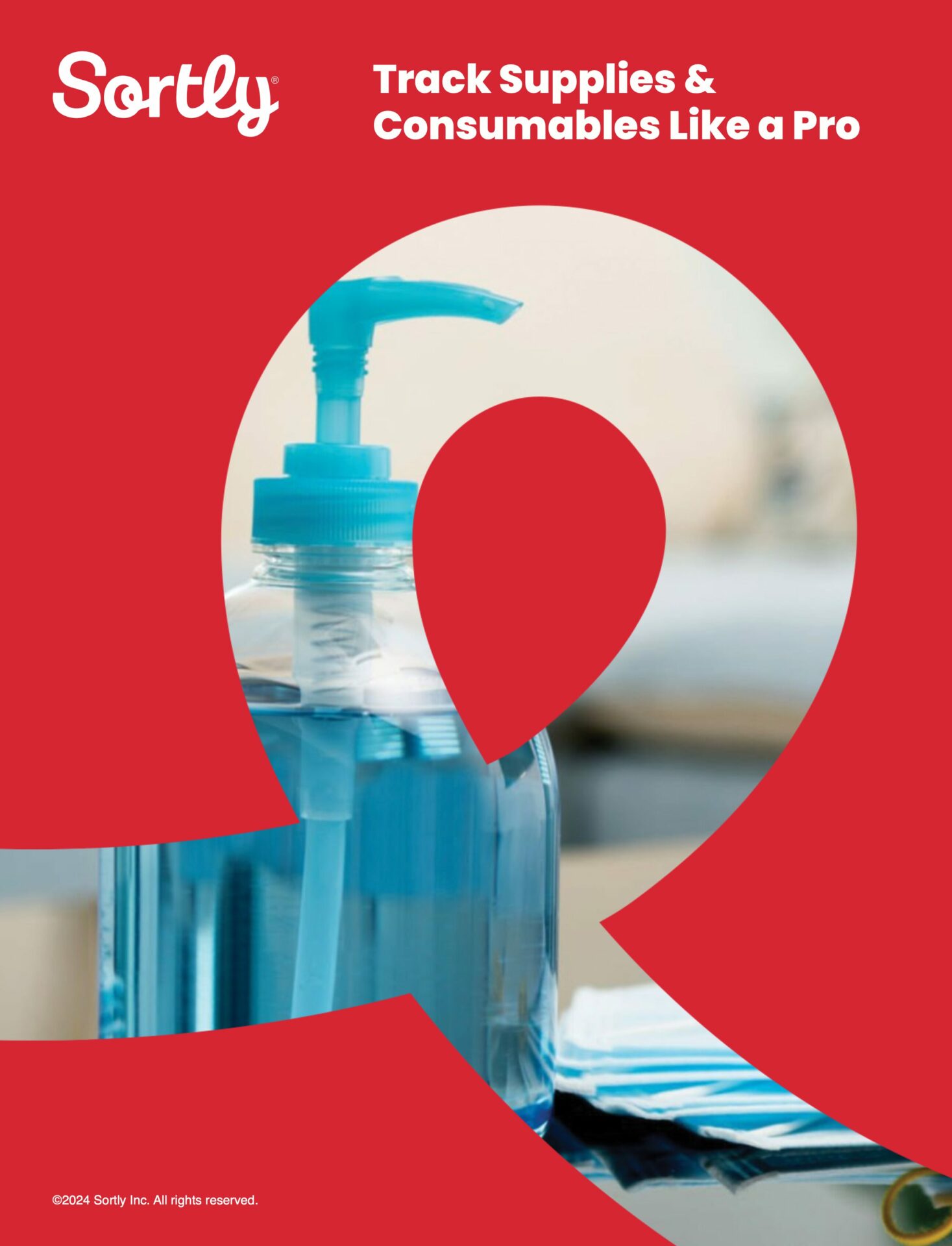
Free Ebook: Track Supplies & Consumables Like a Pro
This easy, comprehensive guide can help you:
- Create an inventory list for supplies and consumables
- Automate reordering with alerts and expiration reminders
- Perform inventory audits for consumable inventory
Warehouse material handling equipment to consider
Many warehouse stakeholders invest in different types of equipment to foster a more optimal handling of warehouse materials. From forklifts to drones, there is no shortage of devices designed to streamline different warehouse activities. Some of the most popular warehouse equipment include:
Percent pallet jacks: These machines are essential in any warehouse where large quantities of inventory are moved. They are necessary for moving heavy loads from one place to another.
Conveyor belts and systems: if your warehouse needs to keep goods moving from place to place, conveyor belts and systems can enhance efficiency while reducing manual labor. This can lower costs while reserving resources for more complicated tasks.
Automated guided vehicles, drones, and picking technologies: Many warehouse stakeholders are also interested in cutting-edge devices that seek, identify, and pick items. As automated technologies, such hardware reduces manual labor by taking over tasks like picking and packing.
Shelves and rocks: While not high-tech equipment, investing in a warehouse’s proper physical and organizational equipment is always a cornerstone of improved efficiency and optimized materials handling. Invest in the right storage solutions to maximize space utilization and foster more efficient and safer materials handling and inventory management.
Loading dock equipment: A variety of assets, including levelers and seals, can ensure seamless loading and unloading of incoming and outgoing deliveries. These devices keep your inventory in good shape, speed up loading dock operations, and keep your team safe.
Best practices for handling materials in the warehouse
When determining how best to handle materials in your warehouse, you’ll need to consider your operation’s unique needs. That said, several agreed-upon best practices are sure to help your organization implement a more robust strategy for handling warehouse materials right away.
1. Develop a standard operating procedure
By creating a detailed guide for handling all warehouse materials, you can ensure consistency and clarity in all operations. This SOP can be used for training, and can also articulate benchmarks and key performance indicators that help keep your warehouse team improving quarter after quarter.
Most warehouses also outline their inventory tracking strategy in this document.
2. Offer regular cross-training
When a new employee is hired in the warehouse, it’s common sense to train them on all things inventory, from materials handling to scanning barcodes and QR codes. That being said, it’s also wise to take the time to cross-train the rest of the warehouse’s employees. The more every team knows about handling materials and equipment, the easier it is to create a workforce that’s scalable, adaptable, and aligned.
3. Practice lean inventory principles
Whether using just-in-time inventory or some other lean inventory strategy, there are various ways to keep less inventory in your warehouse while still swiftly meeting customer demand. These strategies can reduce waste, streamline procedures, and make it easier to maintain an efficient and well-organized warehouse.
Note that to successfully implement a lean inventory strategy, you’ll need an airtight relationship with the rest of your supply chain partners and a near-perfect understanding of future customer demand.
4. Implement stronger inventory control and organization
As mentioned above, a thorough understanding of your organization’s inventory needs can make it that much easier to optimize warehouse materials handling and keep fewer materials on hand. Even if you’re not ready to practice a lean inventory principle, consider improving how your inventory is organized and implementing an inventory control strategy.
Inventory control is the balancing act between keeping enough inventory on hand to meet customer demand without unnecessarily tying up cash in materials your warehouse does not yet need. The more accurate your inventory records, the easier it is to understand inventory usage and to calculate key inventory calculations that inform precise demand forecasting.
5. Emphasize safety above all else
The right technology, in-person training, and checkpoints can ensure your warehouse is as safe as possible. After all, when it comes to handling warehouse materials, you’ll want to ensure that any best practices you implement do not increase the risk of injury to your team.
The right technology can also help you enhance safety and efficiency. For example, using a modern inventory management system, you can add a barcode or QR code to all warehouse equipment. Team members can simply scan the equipment with their smartphones to pull up the item’s inventory profile and learn more about handling and using that asset properly.
An inventory profile can also be used to ensure equipment is properly maintained. What’s more, if you’re using an inventory solution such as Sortly, you can set a customized alert to be reminded when an upcoming maintenance date is approaching, when an asset may be falling out of warranty, and so on.
You should also schedule regular internal reviews and external audits. During these inspections, physically count materials and equipment and search for potential safety hazards and compliance issues. An external consultant can provide additional insight on how to make your warehouse safer, more efficient, and more profitable than ever before.
About Sortly
Sortly is an inventory management solution that helps you track, manage, and organize your warehouse inventory—from any device, in any location. We’re an easy-to-use inventory software that’s perfect for large or small businesses. Sortly builds inventory tracking seamlessly into your workday so you can save time and money, satisfy your customers, and help your business succeed.
With Sortly, you can track inventory, supplies, parts, tools, assets like equipment and machinery, and anything else that matters to your business. It comes equipped with smart features like barcoding & QR coding, low stock alerts, customizable folders, data-rich reporting, and much more. Best of all, you can update inventory right from your smartphone, whether you’re on the job, in the warehouse, or on the go.
Whether you’re just getting started with inventory management or you’re an expert looking for a more efficient solution, we can transform how your company manages inventory—so you can focus on building your business. That’s why over 15,000 businesses globally trust us as their inventory management solution.
Start your two-week free trial of Sortly today.