Most businesses own equipment, machinery, or technology that are long-term assets—investments that your company plans to retain for more than a year. And much of this equipment requires some form of maintenance to stay in tip-top shape. This article will review the five main types of equipment maintenance and zero in on the differences between preventive and predictive maintenance.
What is equipment maintenance?
The 5 types of machine maintenance
There are five machine maintenance types: preventative maintenance, predictive maintenance, corrective maintenance, routine maintenance, and emergency maintenance. Each of these types is essential—but ideally, you’ll be able to avoid corrective and emergency maintenance by scheduling predictive, preventative, and routine service for your equipment.
Here’s a bit more about each of these types of machine maintenance.
1. Preventative maintenance
You’ve likely heard lots about preventative maintenance—inspecting and maintaining equipment at regular intervals so that tiny problems can be addressed before they become big headaches. In a perfect world, preventative maintenance would prevent all breakdowns and malfunctions.
For example, if your business has a fleet of trucks, preventative maintenance would include servicing those trucks and paying for an oil change every 10,000 miles. Sure, your mechanic might find a minor problem during service, but they’ll address it before the truck fails.
Related: How to Keep Track of Equipment Maintenance
2. Predictive maintenance
Predictive maintenance is really more of an evaluation. During predictive maintenance, a person or a machine determines the condition of equipment, then provides an estimate regarding when maintenance should be scheduled.
Predictive maintenance helps companies save money and reduce stress by offering informed advice on when (and what kind) of service machinery or equipment needs.
While skilled trades and technicians conduct some predictive maintenance, many products have built-in, artificially-intelligent systems that offer real-time advice on when and what service to schedule. As machine learning becomes more and more advanced, all kinds of equipment (think tractors, ultrasounds, and even espresso makers) are increasingly monitored by continuous, online systems.
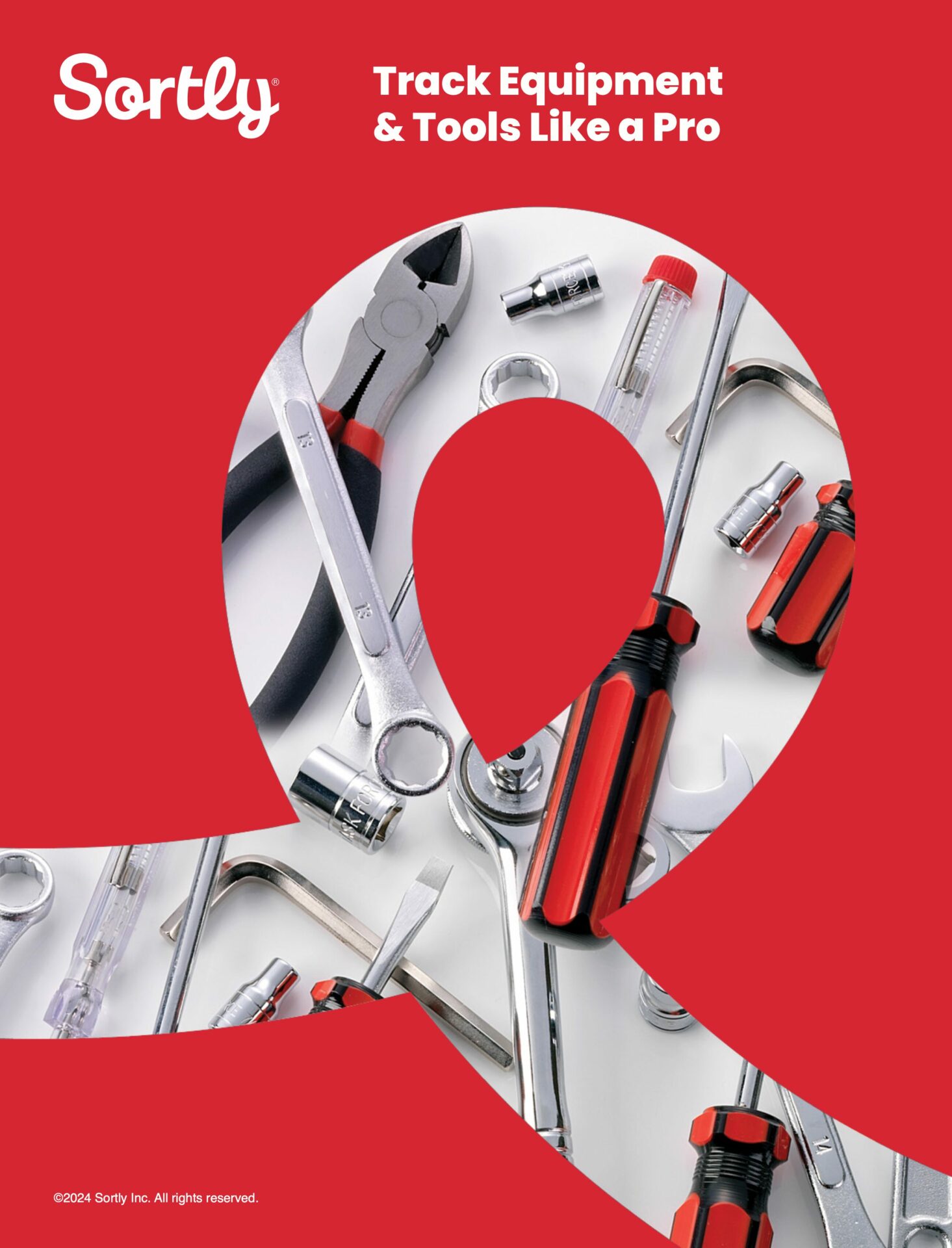
Free Ebook: Track Equipment & Tools Like a Pro
This easy, comprehensive guide can help you:
- Determine which details to track about your equipment and tools
- Set a standard operating procedure for asset tracking
- Perform physical audits of your business’s tools and equipment
Preventative maintenance vs. predictive maintenance
The main difference between predictive and preventative maintenance is that predictive maintenance doesn’t call for maintenance on a set schedule. Instead, predictive maintenance reflects the actual condition of equipment, not best practices.
3. Routine maintenance
Routine maintenance is regularly-scheduled, ongoing maintenance that identifies problems and prevents equipment failure before it’s too late. The term “routine maintenance” is often used interchangeably with “preventative maintenance” since both are planned, scheduled, and intended to solve tiny problems before they become significant issues.
Routine maintenance includes tasks like cleaning machinery and replacing parts that are beginning to deteriorate.
4. Corrective maintenance
Corrective maintenance aims to identify and solve problems with equipment right away. Corrective maintenance is relatively simple—something breaks, and a technician comes out to identify the problem then fix it as soon as possible.
Corrective maintenance can be a quick process, a lengthy one, or something in between. The steps of corrective maintenance are as follows: equipment failure, diagnosis of the problem, fixing or replacing the faulty component, testing the equipment, and ensuring the equipment is working correctly again.
Corrective maintenance can be expensive and cause work stoppages or slowdowns. That’s why so many businesses are keen on preventative and predictive maintenance measures.
5. Emergency maintenance
Like corrective maintenance, emergency maintenance seeks to correct an urgent problem quickly. When emergency maintenance is required, the equipment failure causes either health and safety concerns or an unacceptable dip in productivity.
Emergency maintenance includes gas line leaks, floods, and electrical malfunctions. However, since emergency maintenance is inconvenient and expensive, your business should prioritize preventive and predictive maintenance that can eliminate emergencies in the first place.
Best practices for scheduling equipment maintenance
Since predictive, routine, and preventative equipment maintenance can save your business time, money, and stress, many companies emphasize staying on top of these types of maintenance. Need some tips on scheduling maintenance? These are a few best practices.
Keep a calendar
Whether you use a paper calendar, a digital one, or even a spreadsheet, your business should chart out all preventive and routine maintenance for your equipment, machinery, and technology. Larger companies with multiple locations can create templates for their satellite offices to use.
Experience the simplest inventory management software.
Are you ready to transform how your business does inventory?
Label your equipment
Even though you keep a preventive maintenance calendar, labeling your equipment with information about prior and upcoming services can be ultra-helpful, too. That way, you can conduct a physical audit of your equipment, ensuring nothing got missed or forgotten.
It’s also handy during corrective maintenance—especially if you believe your technician missed a problem or your equipment is under warranty.
Set reminders with inventory management software
With Sortly inventory management software, you can set alerts for critical maintenance and repair dates, such as upcoming preventative maintenance or warranty ends. That way you’ll get a reminder sent straight to your email or in the Sortly app letting you know when it’s time for equipment repair. You can also record or link to your maintenance schedule in each item’s details and attach relevant documents such as warranties and maintenance records.
Related: Sortly for Equipment Inventory Management
About Sortly
Sortly is an inventory management solution that helps you track, manage, and organize your inventory—from any device, in any location. We’re an easy-to-use inventory software that’s perfect for small businesses. Sortly builds inventory tracking seamlessly into your workday so you can save time and money, satisfy your customers, and help your business succeed.
With Sortly, you can track inventory, supplies, parts, tools, assets like equipment and machinery, and anything else that matters to your business. It comes equipped with smart features like barcoding & QR coding, low stock alerts, customizable folders, data-rich reporting, and much more. Best of all, you can update inventory right from your smartphone, whether you’re on the job, in the warehouse, or on the go.
Whether you’re just getting started with inventory management or you’re an expert looking for a more efficient solution, we can transform how your company manages inventory—so you can focus on building your business. That’s why over 15,000 businesses globally trust us as their inventory management solution.
Start your two-week free trial of Sortly today.