Construction projects are notoriously complicated—full of unexpected delays, headaches, and changes. But that doesn’t mean there’s nothing your company can do to address the issues facing the construction industry today.
Some of the pain points construction professionals face are evergreen, while others are more a function of today’s economy, market, and supply chain. Regardless, it’s helpful to know the issues so you can plan for a solution. In this article, we’ll reveal how to address five major roadblocks construction companies face in today’s world.
1. Suboptimal communication
No matter what business you’re in, communication is key. Think about all the people your business needs to communicate with, every day: job site workers, inspectors, suppliers, subcontractors, city employees, customers, designers, architects, and so on.
Fortunately, there are solutions designed to streamline communication between your construction office and everyone else your business needs to contact. You could look into a construction software solution that enables and organizes communication, or you could see how modern communication tools like Slack—or even traditional email—could help your team stay in touch.
No matter what you choose, consistency is key. Your team needs to know how they’re expected to communicate with each other. Having those expectations spelled out will ensure faster communication (and better record-keeping) between everyone collaborating on a given project or job.
Related: 5 Must-Have Apps for Your Construction Business
2. Poor planning
Construction isn’t for the faint of heart—and every project has its own unique twists and turns. But this doesn’t mean there’s nothing you can do to lower the chances that things will go wrong. In fact, poor planning—or suboptimal risk management—is one of the most common challenges facing the construction industry today.
Fortunately, combating potential problems before they materialize isn’t as difficult as it sounds. To improve your risk management strategy, think through the whole job before you break ground. Compile a detailed list of everything that could go wrong, leaning on your past experience, the current construction climate, and everything from the weather to a not-so-reliable electrician to determine the project’s vulnerabilities. You may want to gather information from your colleagues and employees as well to ensure you have as much perspective as possible.
Once you’ve gathered your list, address those items with plans, procedures, and protocols. Replace those weak links whenever possible. And if you can’t, pad the schedule. Allow extra time, and be realistic about permitting, inspections, and delays in receiving supplies and materials. You’ll also want to account for any local challenges, like particularly finicky inspectors, summer hours, and labor shortages.
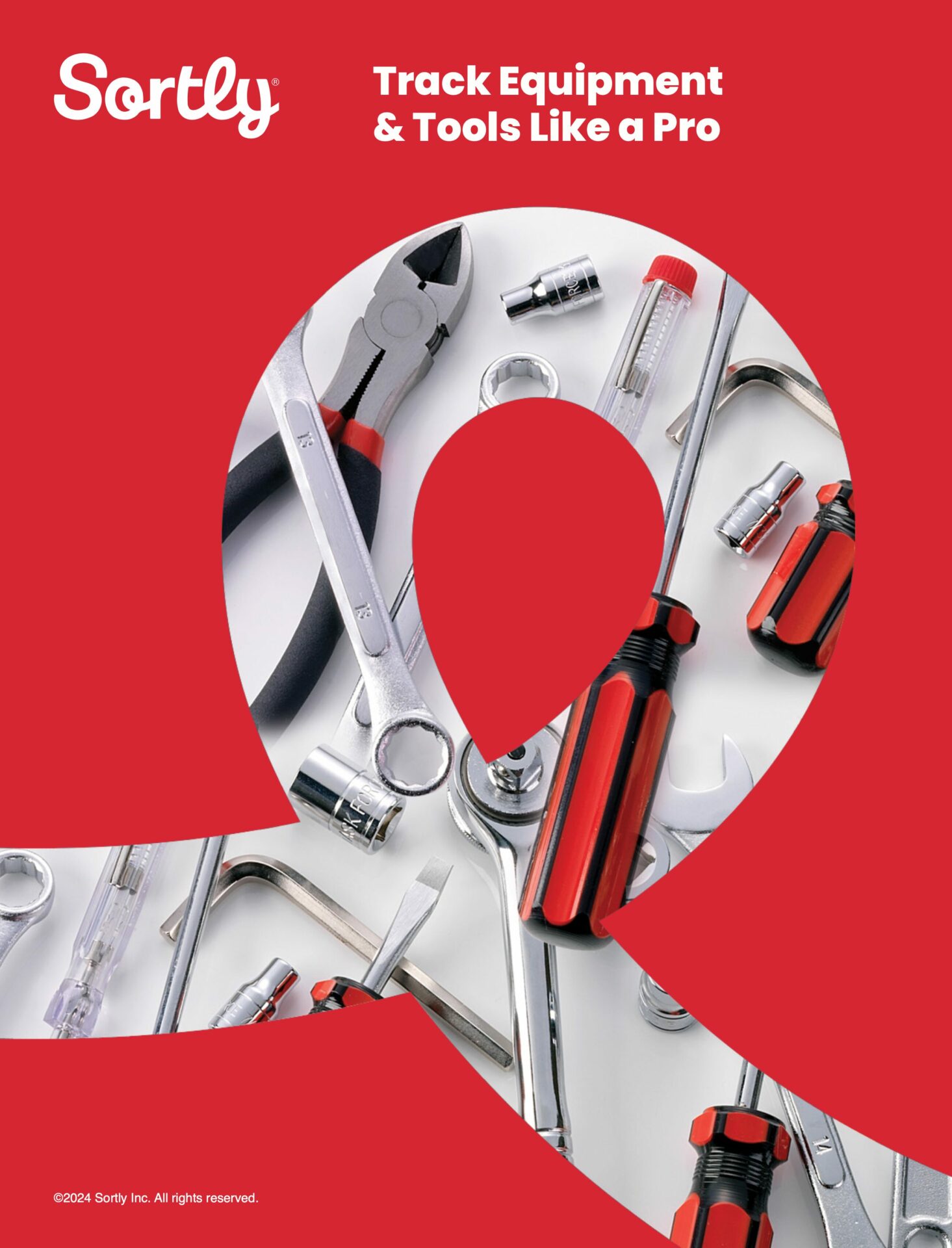
Free Ebook: Track Equipment & Tools Like a Pro
This easy, comprehensive guide can help you:
- Determine which details to track about your equipment and tools
- Set a standard operating procedure for asset tracking
- Perform physical audits of your business’s tools and equipment
3. Supply chain woes
As a construction professional, you already know all about special orders and hard-to-get materials. But now, with an especially stressed global supply chain, it can be hard to get your hands on even the most common of construction materials. Engineered hardwood, floor tile, roofing materials, and even drywall may be hard to come by. And even if you find these items, chances are they cost more than they used to.
What can you do to combat this? First, think ahead. You may need to wait months to receive items you used to order with ease. Plan ahead, crafting a detailed materials list of every item you’ll require to finish a construction project. Cross-reference this list with your inventory list, then order everything else you need in a timely fashion. You’ll want to work with suppliers you trust, especially if you’re relying on them to meet tight deadlines.
A modern inventory management tool, such as Sortly’s inventory app, can help you keep track of all your supplies and materials, even as they move from warehouse to truck to jobsite. While patience is the ultimate solution to supply chain issues, you can still make it easier on yourself by staying organized.
Related: 6 Lessons Learned from the 2021 Supply Chain Crisis
4. Labor shortages
It’s no secret that the construction industry is experiencing a significant labor shortage. And without the skilled workers it needs to get things done, some projects are slowing to a crawl while costs go up. In February 2022, the Associated Builders and Contractors stated that the industry would need to add an additional 650,000 jobs over the year to match current demand.
While there’s little your construction company can single-handedly do to solve that labor shortage, what you can focus on is making your company the most appealing place for workers to take a job. That could mean higher wages, more benefits, paid training, and certifications—anything you can do to get an edge on other companies also looking to hire.
Meanwhile, you’ll need to manage your customers’ expectations. As you know, there’s a limit to how quickly work can be completed, especially when there aren’t enough available workers on site.
5. Poor cash flow
Many of the top challenges in the construction industry outlined on this list can be solved using modern technology and tools. But the ability to pay more—for materials, for labor, for technology—matters, too.
For example, to reduce wait times and ensure a smoother construction process, your company may need to order materials for several jobs all at once, well in advance. While this helps keep the jobs flowing, you’ll need to balance how much of your cash flow you’re willing and able to spend upfront. Try to find your sweet spot—where you have enough to get the job done, plus safety stock—but not so much you’re strapped for cash.
And remember, you can always store construction materials for a later date. Just make sure that when you place a big order, there’s enough wiggle room in the bank to cover those costs. You won’t see a dime back on those purchases until you finally invoice your customers.
About Sortly
Experience the simplest inventory management software.
Are you ready to transform how your business does inventory?
Sortly is a top-rated inventory management app designed to help construction companies track their supplies and materials along every step of the way. Whether you need to know what materials were used on a job, what equipment is in storage, or what supplies are in any given company vehicle, Sortly make it easy to track your entire inventory visually—no matter how many locations you have. Plus, with key features like low stock alerts, barcodes and QR codes, and customizable reports, it’s that much easier to forecast costs, organize inventory by job site, and re-order materials and supplies.
Ready to give Sortly a try? Unlock our most powerful features with a free, two-week trial.