You’ve already conquered tracking your tool inventory. So now you’re ready to create a tool crib system—a secure, organized space to store all those tools.
This article will define a tool crib and explain precisely how to set up a tool crib. Plus, we’ll offer some best practices for maintaining an organized, well-stocked tool crib for years to come.
What is a tool crib?
A tool crib is essentially a supply room—but for your construction company’s tools. These large, secure areas are usually fenced in and locked. Inside, tool cribs are well organized and clearly stocked with the most useful tools construction teams need to get everyday tasks done.
Tool cribs are also used by other businesses, like manufacturers and service providers.
Tool cribs can be purchased prefabricated, or your team can build one using everyday materials like chain link fence, shelving, and hooks. Tool cribs sometimes have roofs or are built high enough—often to the ceiling—to deem secure.
How to set up a tool crib
If you’re ready to set up a tool crib for your construction team in order to keep specific tools organized and secure, these eight steps can help you get started. Remember, these steps are general guidelines and can always be further customized for your unique business.
Step 1: Decide what tools you want to keep together
The first thing you’ll want to determine is what tools you’d like to store in your tool crib. Most construction companies keep tools in a variety of places: trucks and vans, additional commissaries or headquarters, and active job sites. You’ll likely want to set up your tool crib at your company’s home base.
Knowing that, think about the most frequently used items you’ll want to keep safe and organized. These could be items that your team reaches for every day as well as high-value items that you don’t want to risk leaving unsecured.
Note: You can make a preliminary list of the items you’ll store in your tool crib now, but we’ll also make a detailed inventory list in step 5.
Step 2: Appoint a tool crib manager
As you make plans to maintain a tool crib, select a team member to act as your company’s tool crib manager. This employee, sometimes known as a tool crib attendant, oversees every aspect of the tool crib, from auditing equipment condition to ensuring other employees maintain a well-stocked, organized storage area.
Depending on the size of your tool crib and how busy your existing team is, you may need to hire someone to oversee your tool crib. Whatever you decide, tool crib inventory software like Sortly can speed up most inventory-related tasks.
Step 3: Purchase or build a tool crib to hold these items
Once you’ve determined what you’d like to keep in your tool crib, you’ll have a better idea of what size crib you need, what kind of shelving and storage you’ll require, and where you’d like to place it.
Remember, you can have your team construct a tool crib custom to your storage space, or you can buy a prefabricated cage to house tools and equipment. You can also pay a tool crib manufacturer to build a customized tool crib.
While a ready-to-install tool crib can be a quick and easy solution to your company’s storage woes, building a customized, secure storage space that meets your unique needs is often a better investment. After all, your team will be tasked with keeping this area perfectly organized, inventoried, and stocked—and the design, flow, and accessibility of the space matters. You want to see everything stored in the tool crib clearly, and building your own storage space ensures you can do just that.
Step 4: Determine the ideal tool crib organization
Step four—figuring out how to organize your tool crib—should really coincide with step three. As you plan out how to build your tool crib or what tool crib to buy, you’ll want to think about how to optimize storage space, too.
Some construction companies install rolling shelves and drawers to make storage easy. Others hang frequently-used tools for easy access. For best results, you’ll want to measure the height, width, and depth of oversized tools and equipment you intend to lock up and build shelving accordingly.
You’ll also want to consult whomever you’ve appointed a tool crib manager about your organization strategy. This point person will be in charge of maintaining optimal inventory management within the tool crib and should be heavily involved in optimizing the tool crib’s storage and organization strategy.
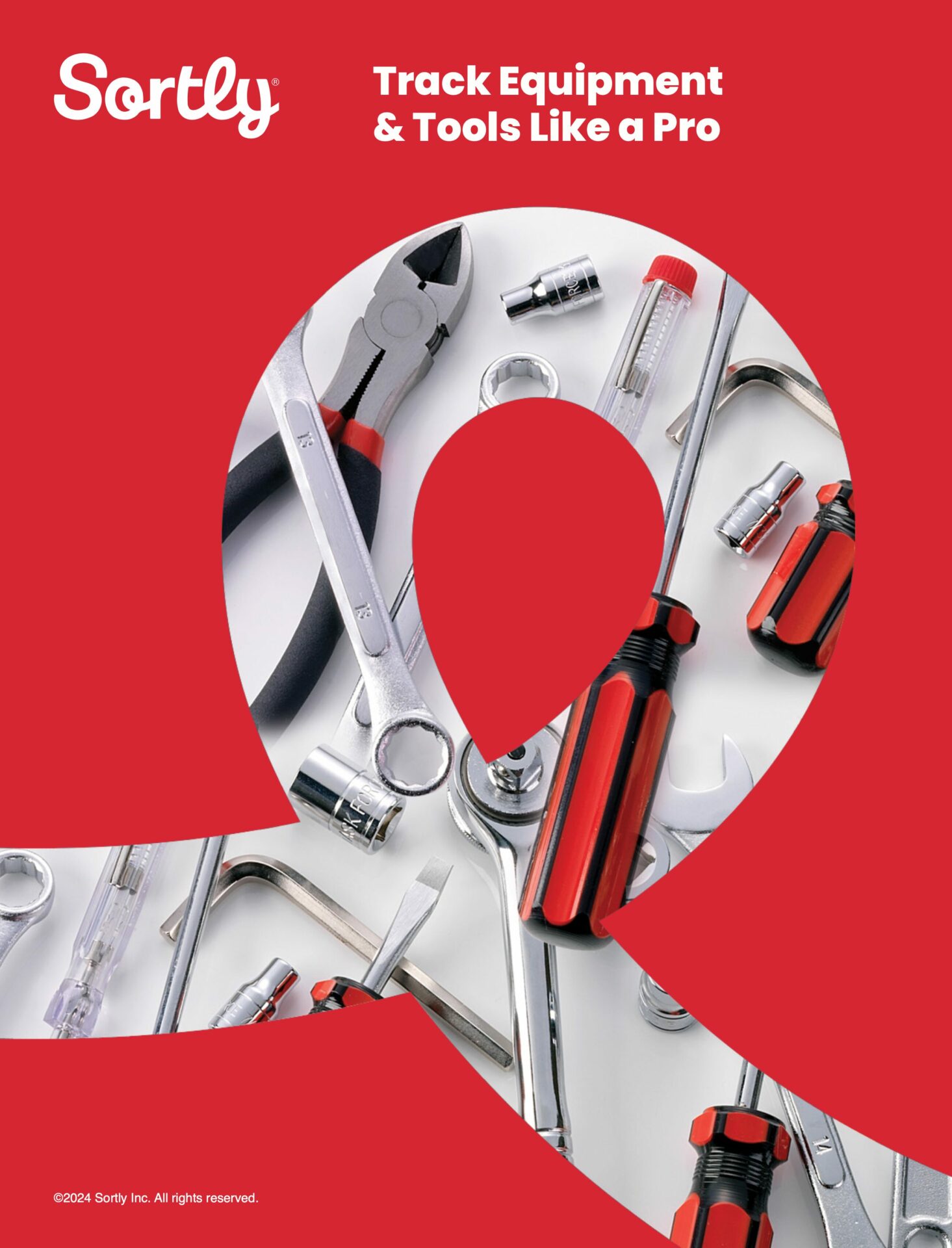
Free Ebook: Track Equipment & Tools Like a Pro
This easy, comprehensive guide can help you:
- Determine which details to track about your equipment and tools
- Set a standard operating procedure for asset tracking
- Perform physical audits of your business’s tools and equipment
Step 5: Pick a tool crib inventory management system
Now that you’ve determined what kind of tool crib you need, who’ll be managing it, what you’ll store in it, and how you’ll organize that tool crib inventory, it’s time to select an inventory management system.
You can keep track of tool crib inventory by hand, using an inventory spreadsheet, or with the help of tool crib inventory software like Sortly. Remember that while every inventory system has its benefits and drawbacks, only inventory software will allow you to automate the checking in and checking out of tools with barcode and QR code scanning—a significant time-saver.
Other benefits of inventory software? High-resolution photos of every item, the ability to drag tools to new locations, low stock alerts, maintenance, warranty end and expiration date reminders, customizable reports, and instant access to your inventory from handheld devices like smartphones and tablets.
Step 6: Create an inventory list—then add barcodes or QR codes
No matter what tool crib inventory management system you choose, you’ll need to create a detail-rich inventory list that catalogs precisely what’s inside your tool crib.
If you choose to use Sortly to manage your tool crib inventory, you’ll be able to add a ton of searchable details to your inventory list, including value, condition, manufacturer, SKU, and more. More importantly, you’ll be able to sync each item to a barcode or QR code for easy checking in and out.
No barcode or QR code on the tool? You can generate a custom code within Sortly, sync it to the tool, and then print out a label to affix to the item.
Ideally, every item in the tool crib should be barcoded for easy inventorying. That way, your tool crib inventory manager and other team members can quickly check items in and out.
Once you’re done updating your inventory list and syncing or creating barcodes and QR codes, create a Sortly folder for all the items in your tool crib. When somebody moves a tool to another location, that inventoried item can simply be dragged from the tool crib folder to a truck or job site folder.
Step 7: Set clear rules for tool usage and item return
Your team has worked hard to set up a tool crib system. But to keep that tool crib organized long-term, your company will need to iron out a standard operating procedure for the tool crib inventory management.
Your tool crib rules for use and return should emphasize organization, accountability, and consistency. For example, if you are using inventory management software, ensure every employee who might use the tool crib has access to a device to check items in and out. Ideally, each user should have their own account to create accountability via activity history.
There should also be clear-cut rules about checking items in and out, whether tools must be returned by the end of the shift—and what the protocol may be if an item needs to be checked out long-term.
You may also want to post a series of questions for employees to answer when they return tools to the tool crib. Questions may include:
- Does the tool require repair, cleaning, or maintenance?
- Has the tool been checked back in via inventory software?
- Was the tool placed in the correct, assigned spot within the tool crib?
Posting these questions can create a sense of accountability and serve as a handy reminder for busy employees eager to move on to their next responsibility.
Step 8: Conduct physical audits and procedural audits
Finally, your tool crib attendant or inventory manager will want to conduct periodic physical audits. By reviewing all inventory by hand, the crib attendant will have an opportunity to double-check the accuracy of the tool crib inventory list and verify the condition of each item in the tool crib.
This audit is also the perfect opportunity to ensure other team members abide by the posted tool crib standing operating procedures.
You can combine your tool crib audit with your regular, year-end inventory audit. You may also want to review whether any new items need to be placed in your tool crib and whether it’s time to expand your tool crib or build another one nearby.
Experience the simplest inventory management software.
Are you ready to transform how your business does inventory?
About Sortly
Sortly is an inventory management solution that helps you track, manage, and organize your inventory—from any device, in any location. We’re an easy-to-use inventory software that’s perfect for small businesses. Sortly builds inventory tracking seamlessly into your workday so you can save time and money, satisfy your customers, and help your business succeed.
With Sortly, you can track inventory, supplies, parts, tools, assets like equipment and machinery, and anything else that matters to your business. It comes equipped with smart features like barcoding & QR coding, low stock alerts, customizable folders, data-rich reporting, and much more. Best of all, you can update inventory right from your smartphone, whether you’re on the job, in the warehouse, or on the go.
Whether you’re just getting started with inventory management or you’re an expert looking for a more efficient solution, we can transform how your company manages inventory—so you can focus on building your business. That’s why over 15,000 businesses globally trust us as their inventory management solution.
Start your two-week free trial of Sortly today.