This article focuses on the role of QR codes in the construction industry, including how they assist with project documentation, safety and inspection processes, and inventory management.
Construction QR codes at a glance
Quick response (QR) codes can help construction professionals stay organized and efficient. While the technology was initially developed to expedite automotive manufacturing, QR codes have become widely adopted across many industries, including construction.
A data-rich upgrade from the traditional barcode, QR codes are read by smartphones and other scanning devices. QR codes store more information and are easier to scan from different angles than barcodes, making them ideal for on-the-job use cases.
In the construction industry, QR codes enable equipment tracking, detailed project documentation, safer work procedures, optimized inventory management, and improved project collaboration.
Common use cases for QR codes in construction
The following five use cases are some of the most popular ways construction companies utilize QR code technology.
1. Equipment and asset tracking
QR codes enable construction companies to rapidly track equipment and assets, even when these high-value items are stored across dozens of job sites and storage locations. Affixing a QR code to physical assets and equipment lets everyone in your crew check assets in and out, enabling you to track who’s using it and where in real time. You can track everything from small handheld tools to large assets like forklifts and tractors.
This process leads to increased visibility, reducing the risk of equipment loss and theft while saving time and money.
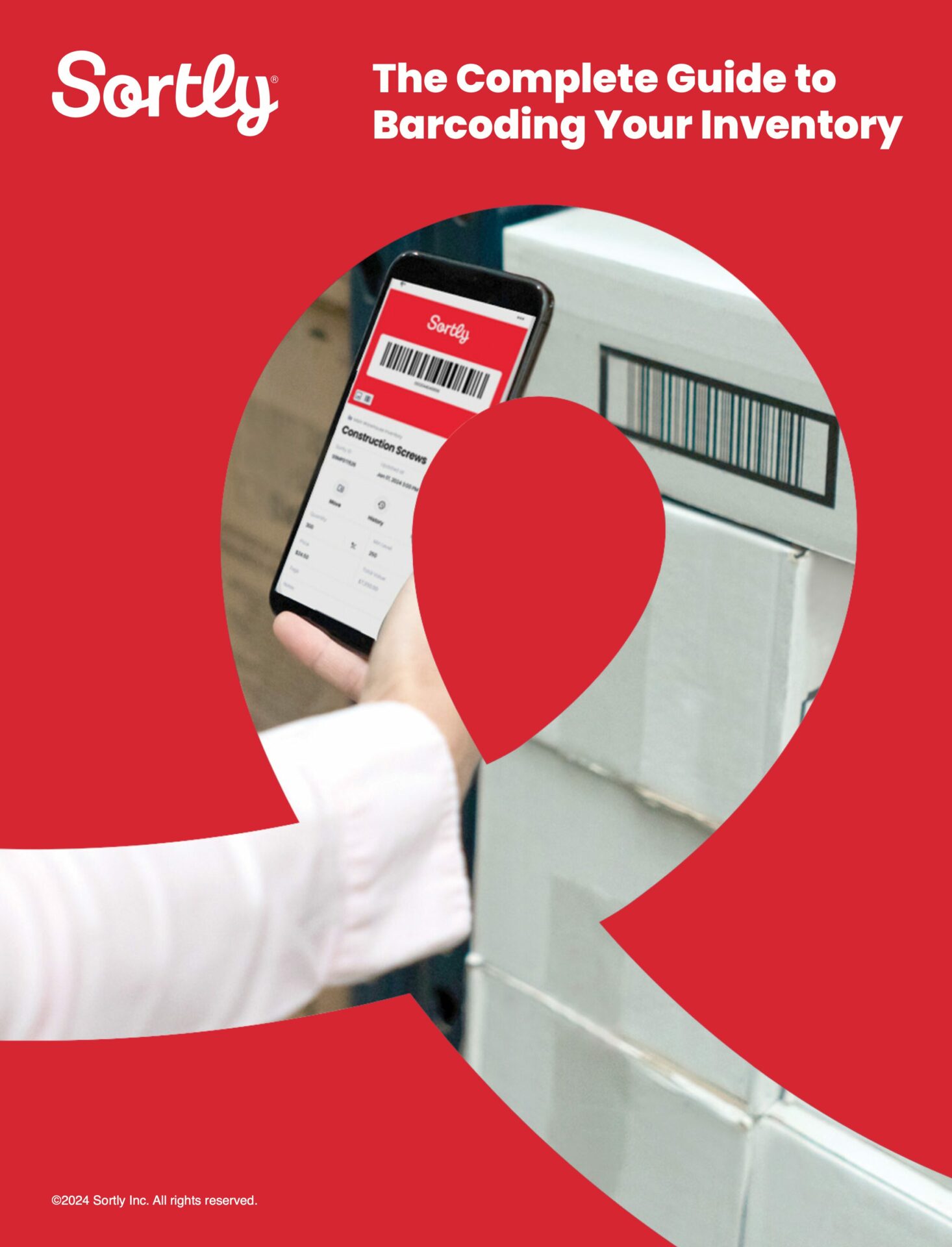
Free Ebook: The Complete Guide to Barcoding Your Inventory
This easy, comprehensive guide will help you:
- Implement a barcode inventory system for your business
- Generate your own unique barcodes
- Practice perpetual inventory control with barcoding
2. Project documentation and information management
By linking QR codes to project documentation, job specifications, and other relevant job-related resources, your team can instantly access essential information about job details just by scanning the code. While in the past, outdated or inaccurate documentation may have circulated on a job site, QR codes make it easy to ensure the data linked to a code is updated.
Whether documentation includes installation instructions, permitting steps, or blueprints, QR codes help reduce costly errors and rework and ensure the right information is accessible to your crew.
3. Safety and inspection processes
Safety and inspection procedures and checklists can also be linked to QR codes on the job site. This reduces reliance on paperwork likely to be damaged and misplaced and enables faster, more accurate digital compliance checks. By streamlining safety protocols and digitizing inspection processes, construction companies can maintain higher safety standards while keeping a closer eye on job sites.
4. Material and inventory management
QR codes also enable rapid, optimized tracking and managing of construction inventory. Whether your construction company has a handful of ongoing local projects or dozens of builds across an entire region, QR code-enabled inventory management helps track inventory location and quantity in real time.
For example, an employee on one job site can scan a bag of grout to learn how many more bags are available on location and at other job sites, on company cars, or in storage facilities.
These practices can reduce material waste and optimize inventory control, leading to a more sustainable business model and significant material and labor cost savings.
5. Project progress tracking and collaboration
Finally, construction companies utilize QR codes for enhanced progress tracking and real-time communication among team members. When the above four use cases come together, construction becomes more efficient, decisions are made faster, and problems are solved sooner.
What’s more, digital documentation for the above use cases is readily available, creating data that clarifies what’s happened on a given job and provides insight that improves work on future projects.
Implementing QR codes in construction
If and when your business decides to implement QR code technology, understanding how this technology can benefit you and what to look for in a solution is essential.
Identifying use cases and needs
First, determine precisely how QR codes can help your construction company become more organized and efficient. Consider your business’s strengths and weaknesses, company size, and resources. While every company’s needs differ, chances are at least two or three of the use cases outlined above apply to your business.
For example, a small construction company may decide not to digitize its safety and inspection processes but may still determine that a QR code-enabled inventory system is a wise investment.
Choosing the right QR code management system
While there are many QR code management systems out there, Sortly is unique in that it’s a powerful inventory solution with built-in QR and barcoding capabilities. The app is equipped with a QR code scanner that connects instantly with your items in Sortly—enabling you to track your inventory and assets on the job, from any device, in any location. It’s an easy, customizable solution that your whole crew can start using in minutes, which means more time focused on getting the job done right. Sortly also offers a two-week free trial so you can test how it works on the job.
Regardless of which system you choose, it’s important to consider customization options, integration capabilities, whether software allows team members to utilize existing devices such as smartphones and tablets, and how easy to use the solution is. Think about who on your team will use the technology and whether they will utilize it on the go. If so, a mobile solution that works on smartphones and tablets may be better than one that requires a computer. Identify your company’s wants and needs, then weigh those against available resources.
Generating and printing QR codes
When generating and printing QR codes, ensure you have the equipment and supplies necessary to quickly scan and affix QR codes. Whether you plan to attach these codes to inventory and assets or clipboards and breakroom walls, find a solution that works for your business.
Remember that some QR code systems utilize regular printers and label paper. Often, this is a simpler and more scalable solution than a QR code generator that requires a special printer.
Implementing QR code scanning and data capture
Finally, ensure employees understand how to properly scan QR codes using smartphones, QR code scanners, or any other device. The ability to rapidly scan codes while on the job is essential for a truly effective QR code system, so take the time to train employees properly.
For more intuitive QR code management systems, this process should be no more complicated than scanning a QR code for a menu at a restaurant. Still, to ensure you reap all the benefits of QR code implementation, create a standard operating procedure that articulates precisely how your business uses QR codes at every touchpoint.
Best practices and tips for implementing QR codes on construction sites
The following three best practices are widely considered essential to successful QR code strategies:
- Print clear QR codes that are appropriately sized. Take care to ensure these codes do not deteriorate over time. Some companies place QR codes in plastic sleeves or other protective covering to reduce the risk of degradation. This is especially important on active job sites where codes may be exposed to the elements.
- Conduct comprehensive training sessions for all employees to ensure they understand how to scan QR codes, when to scan them, and what to do once they have. While scanning a QR code may be intuitive, you still need to train employees on how to make the most of them.
- Regularly inspect physical QR codes and review the data associated with such codes. Keeping this information updated is one of the key reasons why QR codes are so valuable.
Experience the simplest inventory management software.
Are you ready to transform how your business does inventory?
Conclusion
QR codes help many construction companies become more efficient, more organized, and safer than ever before. By embracing QR codes, your construction company can optimize its daily operations and reduce costs associated with rework, delays, and inventory waste, all while enhancing project outcomes and job site safety.
If your construction company would benefit from implementing a QR code system, try Sortly free for 14 days. Our easy-to-use mobile app lets you and your team update inventory on the job, scan and print QR codes, and track all your inventory and assets in real time. That means you can work more efficiently, plan for jobs better, and serve your customers to their highest satisfaction. Join the over 15,000 professionals who trust Sortly as their inventory management solution and sign up today.