In inventory management, creating a standard set of operational practices allows your business to articulate and share the ins and outs of its inventory management strategy. In this article, we will touch on what a standard operating procedure is, how to make one, how to use that inventory SOP as a training guide and refresher, and how to keep your SOP inventory strategy strong as your business changes and grows.
Finally, we will offer a SOP inventory management template to help you get started.
What is an SOP for inventory?
An SOP for inventory should include:
- How inventory is organized and where it is stored
- What inventory is kept on hand, and what minimum inventory levels are
- How to communicate with and order from suppliers
- When orders are placed and what are those order minimums are
- How to inspect, check-in, and store deliveries
- How inventory is checked in and out (i.e., manually, via barcode or QR code)
- When and how to perform inventory audits
The best standard operating procedures will also include an inventory sidework calendar. The point of this calendar is to define what processes need to be done daily, weekly, monthly, quarterly, and annually to ensure your business’s inventory and assets are kept in the best shape possible.
This is especially helpful if your organization maintains equipment or machinery.
Who needs an SOP for inventory?
Just about every business can benefit from implementing a standard operating procedure for its inventory management strategy. This is largely because, regardless of the shape or size of an organization, implementing a thoughtful and proven inventory management strategy can ensure a business is run as profitably and productively as possible.
This is especially true because a strong standard operating procedure is often the cornerstone of a solid inventory control strategy. In other words, when a business defines what good inventory management looks like for the organization, it will also define precisely how much inventory it needs, when inventory will be reordered and from which vendors, and how to store, track, and audit that inventory to ensure it is utilized in the most efficient and value-driven way.
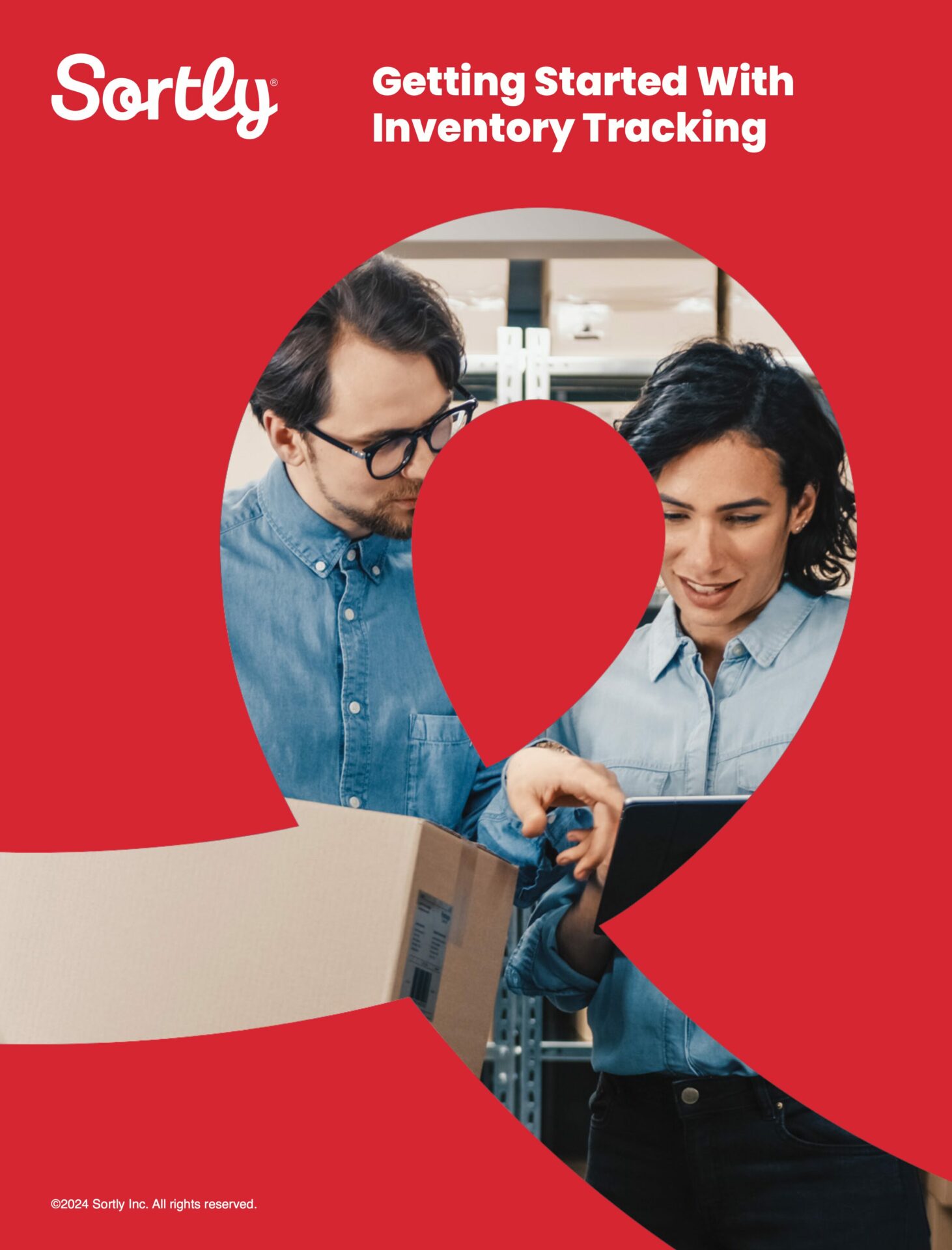
Free Ebook: Getting Started With Inventory Tracking
This easy, comprehensive guide will help you:
- Determine your business's inventory levels and needs
- Organize your inventory for optimal tracking
- Follow tried-and-true best practices for inventory management
How to create an SOP for inventory management
Crafting a standard operating procedure for your organization’s inventory management strategy is a multi-step process. Here are three key steps to drafting your own:
1. Ensure all inventory is organized
Before you begin creating a standard operating procedure, ensure your inventory is physically organized in the most optimal way possible. This may include physically changing how inventory is stored and stocked. Whether that means increasing storage space or investing in smarter shelving equipment, improving the visibility and storage conditions of your inventory can help you understand what inventory you have on hand and enable you to track and audit it much more rapidly.
2. Select an inventory management system
Once your inventory is organized, you’ll want to settle on a way to manage it. You can do this manually, using a spreadsheet, or using inventory software.
A manual inventory system is typically only practical for businesses that stock very few items. A spreadsheet is a significant improvement. However, inventory spreadsheets are prone to human error and corruption. Modern inventory management software is typically considered the best solution for organizations that stock a variety of items, have a lot of inventory that comes and goes, or stock inventory across multiple locations.
3. Record your inventory management practices
However your business decides to track inventory, that precise process should be outlined in detail within the standard operating procedure.
This section should include whether your business plans to practice perpetual or physical inventory tracking. In perpetual inventory tracking, you’ll check items in and out as soon as they arrive, are consumed, or move to another location. On the other hand, if you choose physical inventory, you’ll pick a particular day and time to update inventory records.
In most cases, perpetual inventory is considered the gold standard because it allows stakeholders to monitor inventory levels in real time. That said, it’s nearly impossible to practice perpetual inventory without using inventory management software. The best inventory management software offers barcode and QR code tools that make checking items in and out of inventory a breeze.
If you aren’t practicing perpetual inventory, you’ll want to clarify exactly what your data entry protocols are and when stakeholders can expect inventory records to be updated.
The inventory SOP must also detail your organization’s reordering practices. This includes when orders are placed, with what vendors, what minimum order quantities are, and how inventory should be checked in, inspected, and stored.
Finally, your standard operating procedure should outline how your business performs inventory audits. Whether your company prefers one end-of-year inventory audit or ongoing inventory cycle counts, this process should be fully outlined. This includes providing information on what technology and tools will be used during the audit and what auditors should look for during their counts.
Using your SOP for inventory as a training guide
Once your standard operating procedure is complete, you can use this manual to help onboard new employees and refresh established ones on your inventory management best practices. Ideally, your inventory SOP would be available to all employees at any time, both digitally and physically.
The standard operating procedure can also be used when retraining is necessary. Additionally, as your business grows and scales, and as more information about the efficacy of your inventory strategy is revealed, you should update your SOP to reflect your organization’s current best processes.
If and when you do so, ensure that the updated materials are provided to all employees physically and digitally.
Free inventory SOP template
If you’re looking to craft a standard operating procedure (SOP) for your organization’s inventory management strategy but don’t know where to start, our free SOP inventory template can help.
Free Download: SOP Template for Inventory
Download our free SOP inventory template today! The template is pre-populated with common standard operating procedures for you to customize–feel free to add the procedures and details specific to your business.
About Sortly
Sortly helps you track, manage, and organize all your inventory—from any device, in any location. We’re an easy-to-use inventory solution that’s perfect for small businesses. Sortly builds inventory tracking seamlessly into your workday so you can save time and money, satisfy your customers, and help your business succeed.
With Sortly, you can track consumable inventory like supplies, parts, and raw materials, assets like equipment and machinery, and anything else that matters to your business. It comes equipped with smart features like barcoding & QR coding, low stock alerts, customizable inventory folders, smart reporting, and much more. Best of all, you can update inventory right from your smartphone—and so can your team.
Whether you’re just getting started with inventory management or you’re an expert looking for a more efficient solution, we can transform how your company manages inventory—so you can focus on building your small business. That’s why over 15,000 businesses globally trust us as their inventory management solution.
Start your two-week free trial of Sortly today.