Many businesses, including manufacturers, utilize many raw materials to produce finished products that are later sold to customers. These raw materials, which are one of the four types of inventory, are often basic products that a company would not resell independently but are still crucial supplies that must be inventoried carefully.
In this article, we’ll further define raw materials, then provide you with key details on how to track raw materials using the inventory management system that works best for your team.
What is raw materials inventory?
Raw materials inventory is your company’s stockpile of basic materials that will eventually be used to manufacture a finished good.
Examples of raw materials can be very basic, for example, oil, wood, plastic, coal, and steel. But raw materials can also be parts and pieces that have already been altered or manufactured by a supplier, so long as you use those components to manufacture another finished good.
There are two types of raw materials: direct materials and indirect materials. Direct materials are directly linked to your finished good. For example, if you build a stone-and-steel garden sculpture, both the stone and steel are direct raw materials. But the sealant you used to finish and waterproof the statue is a little less obvious—and considered an indirect material.
Related: Sortly for Raw Material Tracking
Why is tracking raw materials so important?
Tracking raw materials is an essential element of effective inventory management, especially because your business relies on these items to produce finished goods sold to your customers.
If you fail to track your raw materials properly, you risk costly stockouts. And when you run out of the raw materials, you’re not just facing a work stoppage but also the risk that your customers could find another seller, one who’s ready to satisfy their demand sooner.
Tracking raw materials is particularly important to businesses that require hard-to-acquire, expensive, or slow-to-ship products that could be impossible to buy locally—even at inflated prices.
To keep your business profitable and productive, your best bet is to adopt a raw materials inventory management system that ensures you’ve always got exactly what your business needs to manufacture its goods.
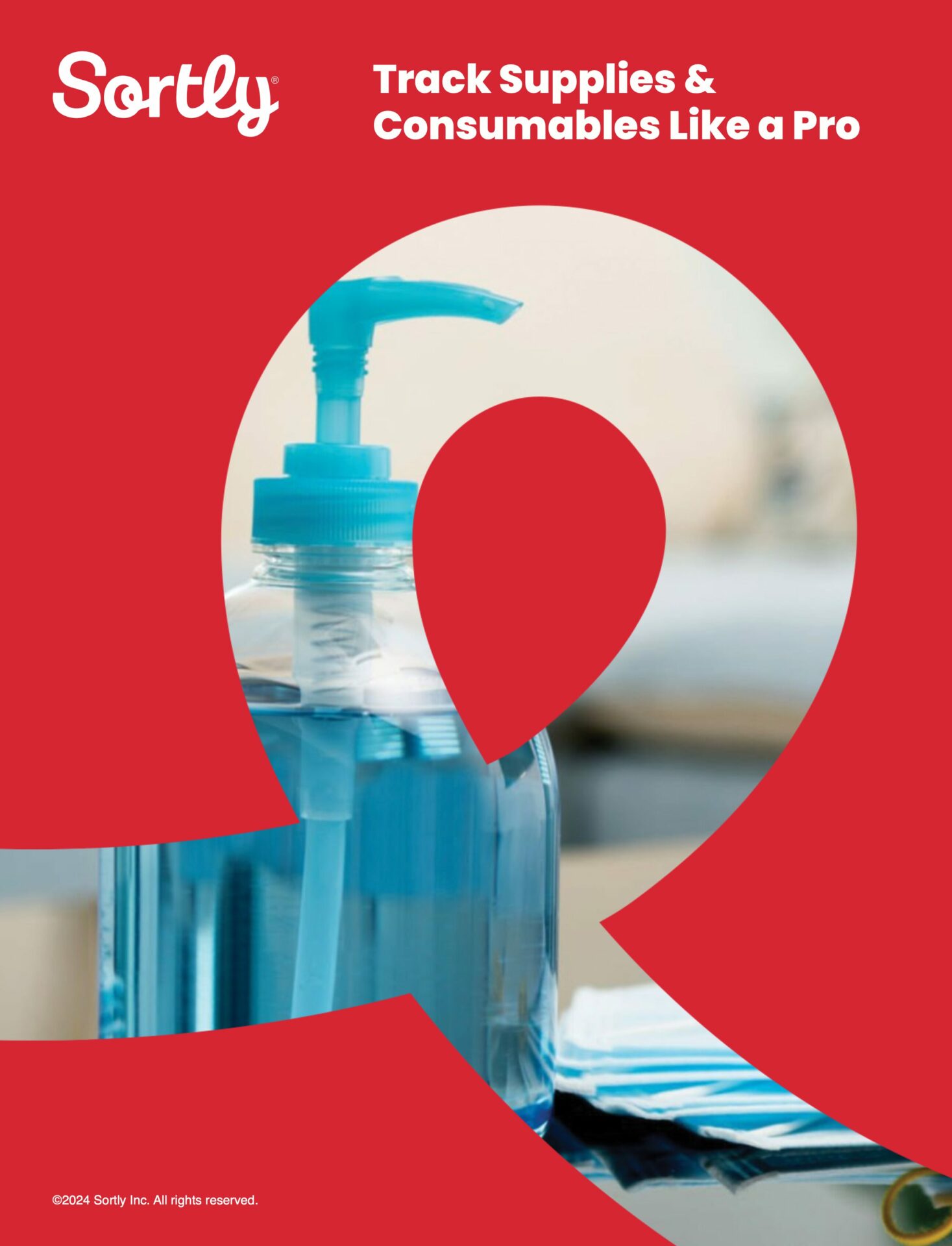
Free Ebook: Track Supplies & Consumables Like a Pro
This easy, comprehensive guide can help you:
- Create an inventory list for supplies and consumables
- Automate reordering with alerts and expiration reminders
- Perform inventory audits for consumable inventory
Challenges of raw materials tracking
While every business is sure to face unique challenges when tracking raw materials inventory, there are a few common pain points worth highlighting.
1. Unpredictability in the supply chain
One challenge of tracking raw materials is setting hard-and-fast reordering rules and inventory minimums when an unpredictable supply chain can throw off even the most organized of business. Your best bet: padding your safety stock during tumultuous times—within reason—and identifying and onboarding backup suppliers ahead of time. That way, they’re ready to assist the moment you need them.
2. Poor employee compliance
Another major challenge of raw materials tracking is employee buy-in. After all, your inventory management strategy is only useful if those tasked with executing it put in the work. The easiest way to address this problem is by choosing the right solution, then offering the right tools and training to support every employee expected to help out.
3. Too much time wasted
Finally, some businesses find that tracking raw materials is time-consuming. This is almost always because a company is tracking inventory manually or with an inventory spreadsheet. Fortunately, inventory apps and inventory management software can automate the most tedious of inventory tasks with features like customizable reports, barcode and QR code scanning, and low stock alerts.
How to keep track of raw materials
Every business should develop its own unique raw materials management strategy based on its specific components, but these five steps offer an excellent foundation for keeping track of your raw materials inventory.
1. Catalog what raw materials your business needs
Managing any type of inventory is impossible if you aren’t sure what your business needs. Before you start tracking inventory, you’ll need to figure out what raw materials you actually need. Take the time to craft a list of every raw material, both direct and indirect, your company uses to produce finished goods. Don’t forget to include items you need only occasionally, especially if you’ll need to special order those products to fulfill requests.
To make this endeavor easier, you can review existing inventory lists, audit what’s on your shelves, browse through old vendor invoices, and talk to your employees about what materials they’re using day in and day out.
2. Develop a perpetual inventory system
If possible, your business should consider keeping perpetual inventory instead of physical inventory. That means that your company will update inventory every time a raw material is received or used up.
This process may seem daunting, but tracking inventory this way doesn’t have to take all day. With the right modern inventory management tools, your team can quickly “check in” and “check out” items using barcodes and QR codes. Inventory solutions like Sortly allow your team to use a phone or tablet as a scanner, and you can also generate custom barcodes and QR code levels for unlabeled inventory.
3. Understand inventory control
While you’re putting together your list of raw materials and considering a perpetual inventory system, you might also want to rethink your inventory control strategy.
Inventory control is all about finding that perfect balance between keeping your inventory costs down and ordering enough inventory to swiftly respond to your customers’ requests. Order too much, and you’ll needlessly tie up cash in raw materials you just don’t need. Order too little, and you run the risk of stockouts and work stoppages that can put a major dent in both your bottom line and your business’s reputation.
And properly tracking raw materials is a huge component of inventory control. After all, one of the most compelling reasons to track what you’ve got and how much of it you use is to save money and order smarter while still putting your company in a position to thrive.
4. Select the right raw materials inventory system
If your team can’t or won’t use your inventory system, then there’s no point in trying to implement it. From the onset, search for an inventory tracking solution that’s in your price range, customizable enough to meet your needs, and user-friendly enough that all your employees can use it.
Think through the equipment and technology you’ll need, too. Some inventory management software, for example, requires external barcode and QR code scanners. Others allow you to use a phone or tablet to perform the same actions. The same goes for keeping inventory on a spreadsheet: will all your employees on the floor have access to a computer, or would some kind of inventory system that works on a phone or tablet be a wiser choice?
No matter what you decide, know that the key to effective inventory tracking is a highly-detailed inventory list. Transform that list of all the raw materials you need into a fully fleshed-out list of every raw material you have on hand, plus anything else you might need to know about it: price, value, location, description, supplier, and more. If you use inventory software, you can also link a barcode, QR code, and any key attachments, photos, or even hazardous materials instructions to the item.
Related: Barcodes vs. QR Codes for Inventory Management
5. Count inventory physically from time to time
One of the major selling points of adopting a perpetual inventory tracking system is that you won’t need to constantly count all the raw materials on your storage shelves. But we still recommend a physical inventory count—or at least a cycle count—from time to time.
An occasional inventory count will allow you to:
- Ensure all inventory-related standard operating procedures are being followed
- Identify inventory loss, then address the problem swiftly
- Reconsider relationships with suppliers should you notice shortages or declining quality
Many manufacturers also conduct an end-of-year inventory count. This audit allows them to unlock the above benefits while also preparing them for tax season and improving their inventory records and demand forecasting numbers.
About Sortly
Sortly is an inventory management solution that helps you track, manage, and organize your inventory—from any device, in any location. We’re an easy-to-use inventory software that’s perfect for small businesses. Sortly builds inventory tracking seamlessly into your workday so you can save time and money, satisfy your customers, and help your business succeed.
With Sortly, you can track inventory, supplies, parts, tools, assets like equipment and machinery, and anything else that matters to your business. It comes equipped with smart features like barcoding & QR coding, low stock alerts, customizable folders, data-rich reporting, and much more. Best of all, you can update inventory in real time, whether you’re on the job, in the warehouse, or on the go.
Whether you’re just getting started with inventory management or you’re an expert looking for a more efficient solution, we can transform how your company manages inventory—so you can focus on building your business. That’s why over 15,000 businesses globally trust us as their inventory management solution.
Start your two-week free trial of Sortly today.