Inventory management is a core component of construction companies. But sometimes that perfect balance of maintaining stock, service, and costs can be challenging. Optimizing inventory levels requires a strategy and implementation that is right for your unique business requirements to keep operations running smoothly, projects on time and budget, and results in high client satisfaction.
This article explores the latest approaches and best practices that the construction industry is adopting to optimize inventory levels at their companies.
Why is inventory optimization important in construction?
There are many reasons inventory optimization is important in the construction industry, including:
Running operations efficiently
When you have clear visibility of construction materials required for your inventory levels, you eliminate unnecessary stock variability and maintain a better inventory balance, even when they’re are multiple warehouse locations.
Eliminating overstocking and understocking
Inventory optimization reduces high carrying costs and wasteful reordering. Having accurate insight into what’s in your inventory prevents “just in case” or future stock. Conversely, you won’t deal with the consequences of stockouts and backorders.
Cutting overall inventory costs
Reducing unnecessary inventory resources means you’ve pulled down the overall inventory cost. You can allocate that money for newer equipment or technology investments that you’ve put off. Even better, you can put it towards revenue-generating activities to engage new clients.
Improved customer satisfaction
When your inventory is optimized, you’ll be ready when customers want to kick off projects with all the materials for the right time and place. They can count on you as a construction supplier to be a reliable vendor to work on their project and boost customer loyalty.
Better time resourcing
Inventory optimization also means employees are working smarter, not harder, as the saying goes. Warehouse personnel can work more efficiently, operations can focus on higher-level responsibilities, and sales can bid out new jobs confidently knowing there is inventory availability.
Improved project planning
Knowing what you have in your inventory provides the foundation for accurate project planning. With deep insight into available stock, you can confidently plan for upcoming jobs without negotiating timelines, budgets, or other sales roadblocks.
Reduced delivery time
Optimizing inventory helps you more easily track and improve delivery times to their ultimate destination. This is a critical component for construction companies to send the right amount of stock to the correct locations, such as another warehouse or multiple job sites, and helps ensure projects are running on time and within budget.
Better collaboration in the supply chain
When you know what inventory is required at all times, working with your suppliers and vendors upstream and downstream becomes easier. You can more accurately predict which orders you will need and when, fulfill deliveries more efficiently, and maintain and build strong vendor relationships.
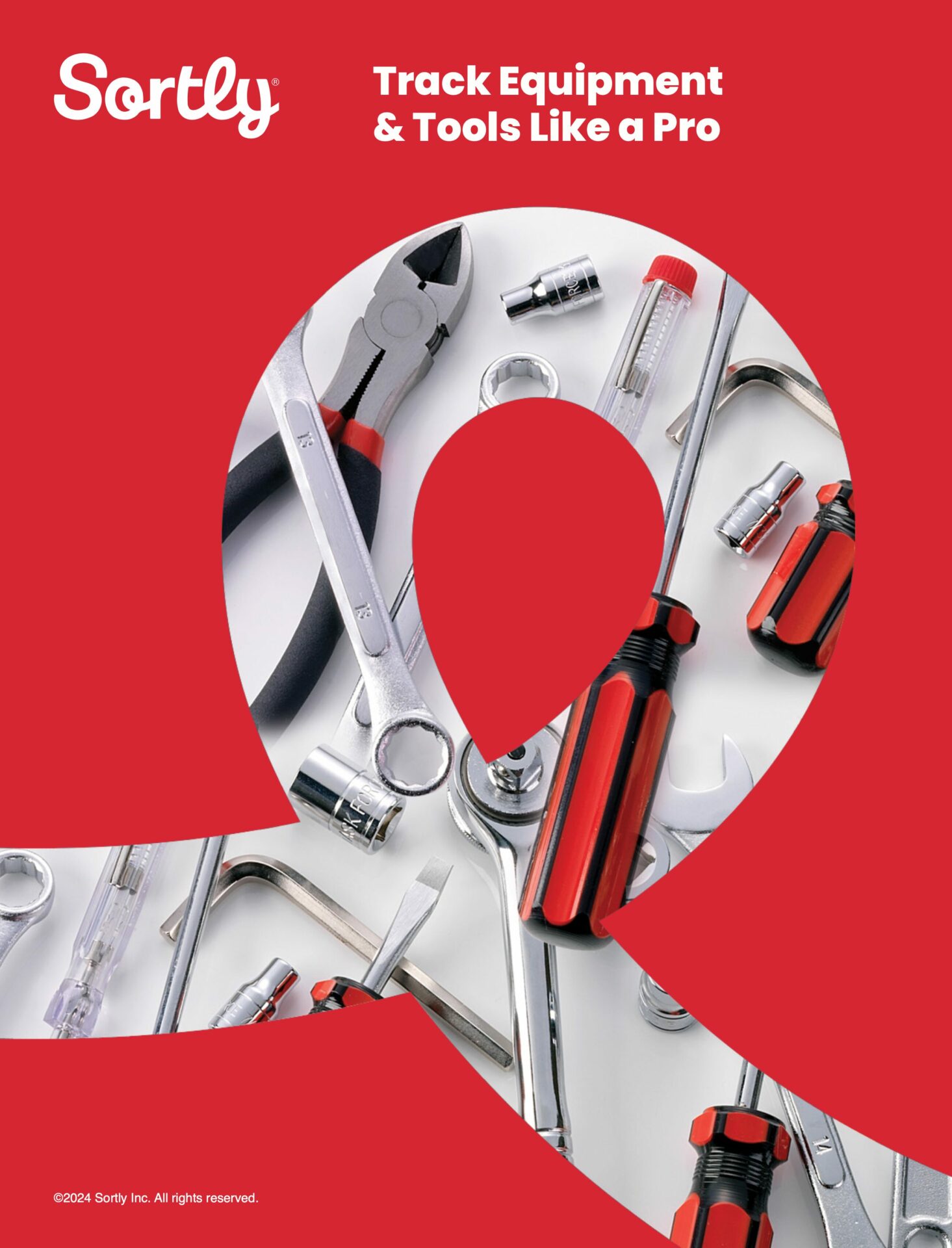
Free Ebook: Track Equipment & Tools Like a Pro
This easy, comprehensive guide can help you:
- Determine which details to track about your equipment and tools
- Set a standard operating procedure for asset tracking
- Perform physical audits of your business’s tools and equipment
Tips for optimizing construction inventory
There are some proven ways to optimize inventory management in construction-related businesses. In some cases, you may want to implement several strategies to maximize the effectiveness or test different methods to see which is most effective for your construction company. No matter which strategies you select, they can help you achieve inventory optimization for your business’s unique needs.
Conduct comprehensive inventory analysis: As a baseline, you can establish the benchmark of your inventory to identify and analyze historical data, consumption patterns and trends, demand fluctuations, and other variables that impact inventory. This detailed analysis can provide key insights into your current inventory management practices, what’s working well, gaps, and other insights.
Just-in-time (JIT) inventory practices: JIT inventory management is a popular method of inventory optimization in the construction industry. The principle of JIT is that you order no more and no less than you need for the demand of the upcoming project. This helps minimize storage costs, reduce inventory holding times, and help foster good vendor and supplier relationships.
Demand forecasting: Demand forecasting relies on analyzing past sales, consumption or other relevant data sets to predict what future demand for the construction product or service will be. Some methods include analyzing industry/macroeconomic factors, short-term and long-term analysis, and other formulas. With so many demand forecasting methods, construction companies often use multiple techniques for discrepancies or fine-tuning results.
Inventory production quantity: Also known as economic order quantity (EOQ), this technique of inventory tracking technique relies on knowing exactly how much product a company should order to meet customer demand while minimizing holding and ordering costs This model works best for businesses with consistent and predictable stream of business.
ABC analysis: The ABC analysis method focuses on which inventory parts should be prioritized based on their importance. The ABC, as indicated in the name, divides your business’s inventory into three categories: A (highest priority), B (next highest), and C (lowest). It will tell you your most and least revenue-generating products and which ones to prioritize as high-demand stock.
Automated replenishment: The automated stock replenishment technique relies on software data analysis of inventory levels, lead times, and sales history to optimize reorder levels to purchase from suppliers. It doesn’t include an actual inventory count but manages the entire process through technology.
How inventory management software helps optimize inventory
Inventory optimization can take some effort and time to reevaluate how your construction company stores, orders, counts, and organizes stock. But the payoff will be worth it in the long run. That’s why it’s critical to find strategies and solutions that work for your company.
The right balance of enough inventory to meet the demands of your upcoming projects results in increased efficiency, better resource management, more happier and loyal customers, and ultimately, more business profitability.
If your company would benefit from improved inventory management, try Sortly free for 14 days. Sortly lets you organize, track, and manage your inventory—from any device, in any location. Our easy-to-use mobile app lets you and your team update inventory on the job, scan barcodes from your smartphone, set low stock alerts to remind you to re-order, and more. That means you can work more efficiently, plan for jobs better, and serve your customers to their highest satisfaction. Join the over 15,000 professionals who trust Sortly as their inventory management solution and sign up today.