For many construction professionals, keeping track of tools isn’t just a challenge—it’s downright stressful. Fortunately, learning how to track your tools doesn’t have to be complicated. This article will reveal how to inventory your tools so the process is efficient, accurate, and frustration-free.
Additionally, we’ve included a free download of our tool tracking spreadsheet to help you start tracking your tools today.
5 Steps to Tracking Your Tools
Your team of construction professionals needs a fully-stocked suite of tools to effectively complete construction jobs. What’s more, your team needs a well-organized tool system if they want to avoid wasting time searching their toolbox, kit, crib, or vehicle for the right inventory.
By tracking your tools in real time, you and your team will always know where to find that spray gun or electric sander. Plus, it’ll be easier to keep track of important maintenance dates, high-value tools, warranty end-dates, and tools that change hands frequently.
To start tracking your tools, try implementing this five-step system:
1. Make a list using an inventory management system
Your company will want to decide on an inventory management system to organize your tools from day one. There are three main ways to keep track of inventory: by hand, using an inventory spreadsheet, or with the help of inventory management software.
For most businesses, using an inventory app like Sortly is the most effective solution. That’s because inventory software offers many powerful automation features that make construction inventory management that much easier. These features—including barcode and QR code syncing and scanning, low stock alerts, and customizable reports—will enable you to complete the next four steps without friction.
And, no matter what method of managing inventory you choose, you’ll need a detail-rich inventory list to keep track of your construction company’s tools. Remember, your inventory list should include all the information you need about the tools you keep on hand, from location to value to SKU. Using an inventory app like Sortly, you can also add high-resolution item images to the database. This can help you clarify which item you are referring to and can even document item condition.
Related: Using Sortly for Tool Tracking
2. Add barcodes and QR codes to tools
Now that you’ve compiled an inventory list, you’ll want to sync or generate barcodes and QR codes for all the items on your list. This step is only possible if you’ve adopted an inventory management system that allows barcode and QR code scanning, such as Sortly.
What makes barcode and QR codes helpful for tracking tools? When using inventory software, employees can simply scan the tool’s barcode with their smartphone to update quantities, edit item details, or change the item’s location instantly. Employees can check tools and equipment in and out, creating a transparent record of who had what and when. For Sortly users, creating and printing barcode labels is easy to do and requires no special equipment.
Once you’ve implemented a QR code or barcode inventory system, your team can track inventory as items are consumed, sold, or moved from one location to another in real time. This will help you practice better inventory control, especially on frequently used items, inventory that moves around a lot, or high-value stock.
Without barcode and QR code scanning, construction employees will have to physically account for tools at times like the end of the day, workweek, or even month or quarter. This delayed strategy can lead to confusion about where tools are and can also inadvertently lead to inventory shrinkage.
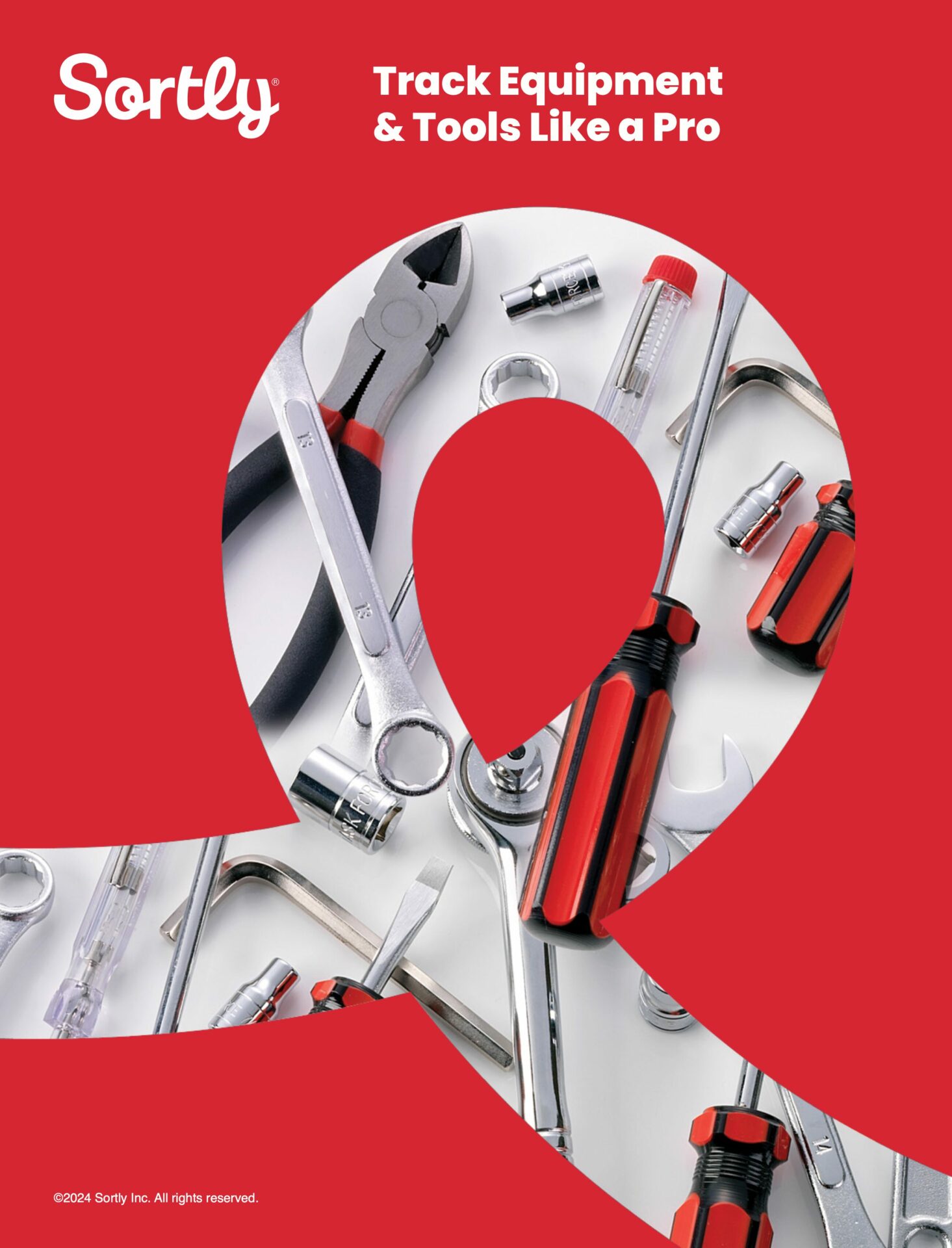
Free Ebook: Track Equipment & Tools Like a Pro
This easy, comprehensive guide can help you:
- Determine which details to track about your equipment and tools
- Set a standard operating procedure for asset tracking
- Perform physical audits of your business’s tools and equipment
3. Consider categorizing, bundling, or “kitting” tools
Chances are, many of your tools fall under certain categories that could make organizing and tracking them easier. For example, there are likely tools every employee needs for every job. And then, on top of that, there are tools required only for drywalling, tools only needed for refinishing hardwood floors, and tools only required for demolition.
Take some time to determine how to best categorize the tools your company keeps in stock. Sortly users can bucket inventory using “categories” or “tags” or even drag items into corresponding folders based on tool cribs or fleet vehicles.
You may also decide that categorizing tools isn’t enough, and you’d like to physically keep them together, too. If that’s the case, you might consider kitting your inventory. By bundling inventory, you can combine a set of frequently used tools into one “kit.” You can even create a barcode or QR code for the kit. This can be helpful for toolboxes or sets that employees grab before heading out to a job site.
4. Track items as they move to different locations
Whether or not you bundle tools, it’s essential to set up a standard operating procedure for tracking all tools as they change hands and move from storage to truck to job site. That way, you’ll always know what tools you have, where they are, and what condition they’re in.
Sortly makes this easy by allowing you to set up folders by location. That means you can have a dedicated folder for each job site, warehouse, vehicle, and more. All your employees need to do is move the item in Sortly based on where the tool physically is. You could also track this manually in different tabs on a spreadsheet.
Tracking inventory by location is important for all businesses, but it’s especially crucial for construction companies, especially large ones. For example, if you run a construction company that offers services all over the state of Florida, you’ll want to keep tabs on inventory at every location, job site, and company truck—even if your inventory manager never actually visualizes this inventory.
Encouraging your employees to practice perpetual inventory and correctly update inventory software every time an item is moved, used, or restocked will help your construction company remain properly stocked and efficient.
5. Set up a system for auditing
Managing your tool inventory is an ongoing process, and when tools go missing, construction work slows down and stops. That’s why auditing inventory, even when a great perpetual inventory system is in place, is crucial.
End-of-year inventory counts are recommended for even the most diligent construction companies, but many others perform inventory cycle counts or randomized audits occasionally to ensure all items are exactly where they’re supposed to be. The stronger your tool-tracking strategy, the less frequently you’ll need to perform such audits, and the less likely you are to uncover missing or damaged stock during these counts.
Free Tool Tracking Template
If you’re not ready to use a mobile inventory app for tracking tools quite yet, a tool tracking Excel spreadsheet is a solid place to start. Use this template as a starting point for listing the tools you have on hand and then customize it to meet your company’s unique needs. You can always “bulk upload” the data to an inventory app later if and when you’re ready to digitize your tool-tracking strategy.
Download: Tool Tracking Excel Template
About Sortly
Sortly helps you track, manage, and organize all your inventory—from any device, in any location. We’re an easy-to-use inventory solution that’s perfect for small businesses. Sortly builds inventory tracking seamlessly into your workday so you can save time and money, satisfy your customers, and help your business succeed.
With Sortly, you can track consumable inventory like supplies, parts, and raw materials, assets like equipment and machinery, and anything else that matters to your business. It comes equipped with smart features like barcoding & QR coding, low stock alerts, customizable inventory folders, smart reporting, and much more. Best of all, you can update inventory right from your smartphone—and so can your team.
Whether you’re just getting started with inventory management or you’re an expert looking for a more efficient solution, we can transform how your company manages inventory—so you can focus on building your small business. That’s why over 15,000 businesses globally trust us as their inventory management solution.
Start your two-week free trial of Sortly today.