It’s no secret that Sortly’s barcode and QR code features are some of our customers’ favorite offerings. After all, barcodes and QR codes are essential for automating inventory management strategies and keeping inventory lists accurate in even the fastest-paced of industries.
This article will touch on how different Sortly customers use barcodes and QR codes to streamline their inventory management strategies across various industries and use cases.
1. To assign and create barcodes for unlabeled inventory
Many Sortly customers maintain inventory that does not come with a manufacturer’s barcode or QR code. As a result, when these customers first set up an optimized inventory system, it’s essential they label each item with a barcode or QR code. Otherwise, it’s impossible to practice perpetual inventory.
That said, manually creating barcodes and QR codes for unlabeled stock can take days if not more. Fortunately, Sortly automates this process by rapidly generating customized barcodes and QR codes that instantly sync to items’ profiles.
“Sortly checks all the boxes for a good inventory management system. The mobile app is great and the system allows you to assign and create barcodes to items.” – Will N.
Another Sortly customer agrees, mentioning that their business can decide whether to create their own barcodes or allow Sortly to automatically generate and assign them to items.
“I love that we can assign our own barcodes or Sortly will make them up for us.” – Lisa D.
2. To print custom barcodes and QR codes without frustration or additional equipment
There are many ways to generate a barcode and QR code, and just as many ways to turn those codes into labels you can print and affix to inventory. That said, one of Sortly’s most treasured features is its one-step, frustration-free, in-app barcode and QR code generator.
Customers appreciate that they don’t need to purchase or rely on additional software to create codes, and that whatever codes they create are automatically synced to the correct items.
Additionally, creating customized labels is a breeze. Customers can select what information they want printed on the barcode or QR code label, then use regular printers and ordinary label paper to create the inventory stickers.
Once all inventory is labeled correctly, customers can use Sortly’s in-app barcode and QR code scanner on their phones or tablets to check items in and out or learn more about a product. No additional hardware is required: not to generate or print the codes, and not to scan them.
“I like the ability to scan and easily print QR codes.” – Christin S.
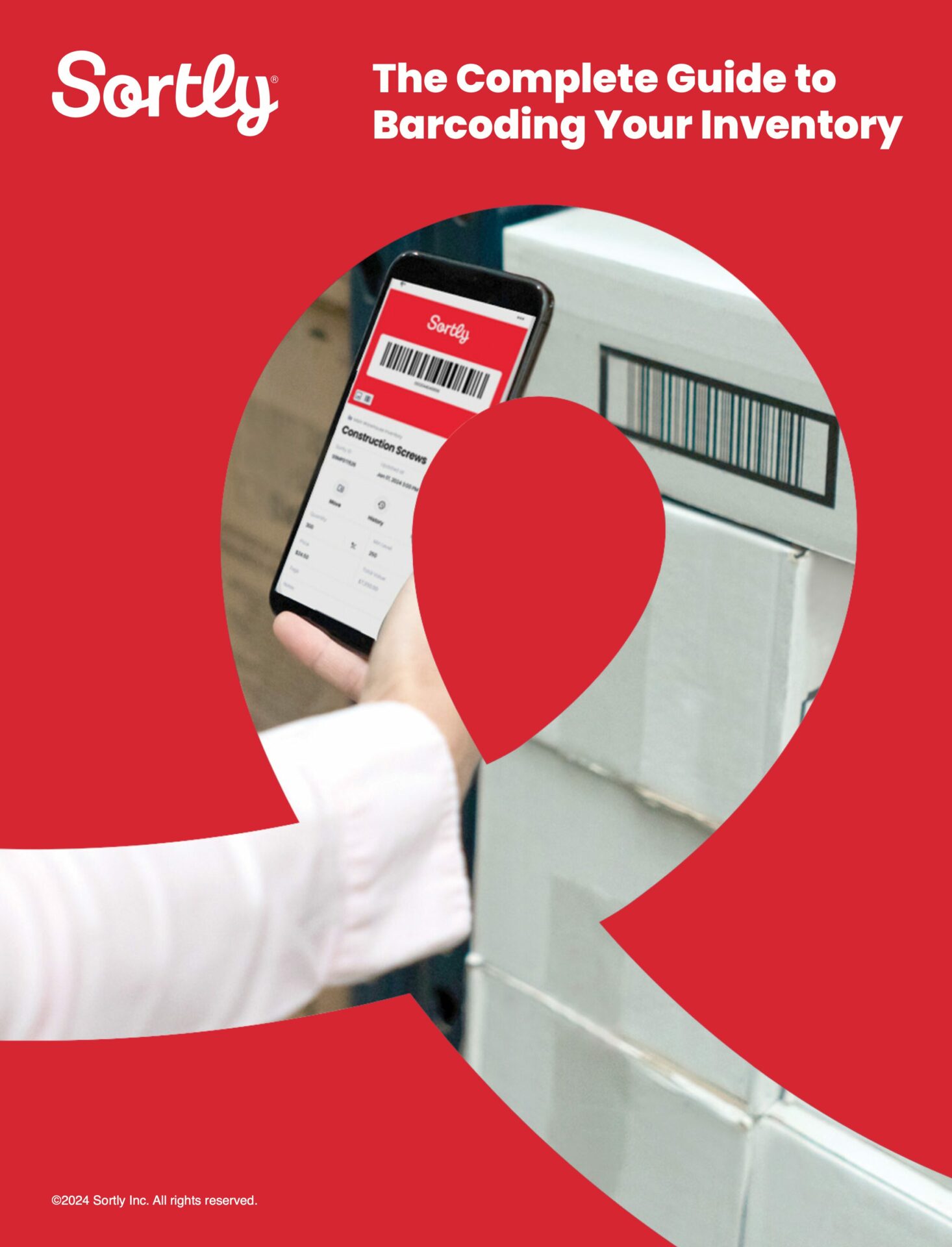
Free Ebook: The Complete Guide to Barcoding Your Inventory
This easy, comprehensive guide will help you:
- Implement a barcode inventory system for your business
- Generate your own unique barcodes
- Practice perpetual inventory control with barcoding
3. To enable better productivity on the job through “scan-and-go” strategies
Many Sortly customers, especially those who work in industries like plumbing, engineering, and construction, rely on Sortly to streamline the tracking of inventory when items are rapidly moved from a warehouse or storage facility onto a truck or to a job site.
One Sortly customer, whose review is highlighted below, appreciates the ability to connect picture-rich item profiles to QR codes that drivers can rapidly scan to check items out before beginning their day. This is a chief tenet of perpetual inventory management and allows businesses of all shapes and sizes to know exactly what inventory is on hand, where it is, and how much of it they have.
“I downloaded this app, and within two hours, our intern had the entire inventory organized—with pictures! Possibly the best part is it creates QR labels for all your items so the driver can just scan and check out a box. Absolutely perfect. Wish I’d found this years ago.” – Bandisahn
4. To keep track of tens of thousands of items
Another Sortly customer, Bilo Plumbing & Heating, relies on QR codes for significant, real-time inventory tracking. The business’s warehouse houses over 52,000 parts, and each of the company’s trucks carries 10,000 parts alone.
To manage and track all this inventory effectively and accurately, the business relies on Sortly’s QR code generator and scanner. Each QR code is generated and printed through Sortly and includes the manufacturer’s name, item description, and part number.
“We have a QR code on everything.” – Jonathan S.
About Sortly
Sortly is an inventory management solution that helps you track, manage, and organize your inventory from any device, in any location. We’re an easy-to-use inventory software that’s perfect for large or small businesses. Sortly builds inventory tracking seamlessly into your workday so you can save time and money, satisfy your customers, and help your business succeed.
With Sortly, you can track inventory, supplies, parts, tools, assets like equipment and machinery, and anything else that matters to your business. It comes equipped with smart features like barcoding & QR coding, low stock alerts, customizable folders, data-rich reporting, and much more. Best of all, you can update inventory right from your smartphone, whether you’re on the job, in the warehouse, or on the go.
Whether you’re just getting started with inventory management or you’re an expert looking for a more efficient solution, we can transform how your company manages inventory—so you can focus on building your business. That’s why over 15,000 businesses globally trust us as their inventory management solution.
Start your two-week free trial of Sortly today.