Managing equipment inventory properly is crucial to any business that relies on machinery, technology, or other assets to perform services or produce goods for customers. By ensuring equipment inventory is organized, documented, properly tracked, strategically located, and well-maintained, businesses can operate with confidence while protecting high-value assets from loss, damage, or theft.
This article will focus on four best practices for equipment inventory management.
What is equipment inventory management?
Equipment inventory management is important whether you run an office or a highly specialized business. For instance, equipment assets may include technological hardware, like computers and tablets; machinery, such as factory equipment; or construction assets, like cranes, tractors, and chainsaws. In the medical field, equipment may include ultrasound machines and surgical beds.
Every company maintains a different list of equipment inventory, but regardless of industry, businesses need to employ an accurate and effective equipment management system. Equipment is often worth tens of thousands of dollars, and each asset’s location, condition, and maintenance schedule can affect a company’s short-term productivity and long-term profitability.
By employing the following equipment management best practices, businesses can keep better track of assets, optimize productivity, and ensure all equipment is maintained correctly.
Experience the simplest inventory management software.
Are you ready to transform how your business does inventory?
How to manage equipment inventory
The following four best practices help businesses maintain a more accurate and effective equipment inventory list.
1. Select the right equipment management system
There are three ways to track inventory: manually, on a document or even a sheet of paper; on a spreadsheet; or using equipment inventory management software.
Manual inventory management is typically only successful for very small businesses that maintain an inventory list that’s under a single page long. It’s virtually impossible for companies that track inventory across multiple locations to track items manually.
While spreadsheet inventory management, especially when stored on the cloud, is easier to keep synced, spreadsheets are prone to human error, especially during data entry. This is particularly true if many items kept on hand have similar names. Because it’s so difficult to display images on a spreadsheet, it can be easy for team members to confuse similarly named items, resulting in widespread inaccuracies across cells and sheets.
As a result, more and more companies have been using inventory management software such as Sortly to keep track of their equipment. Sortly is an easy equipment management system that allows businesses to track, manage, and organize inventory—even if inventory is stored across multiple locations.
Once you have your equipment logged in Sortly, keeping track of equipment in real time is simple, and anybody on your team can access inventory data on the go using simple devices like a smartphone, tablet, or computer. Equipment inventory can be managed, tracked, searched, or checked in or out from any location with Sortly—and it’s so easy that there’s no training required.
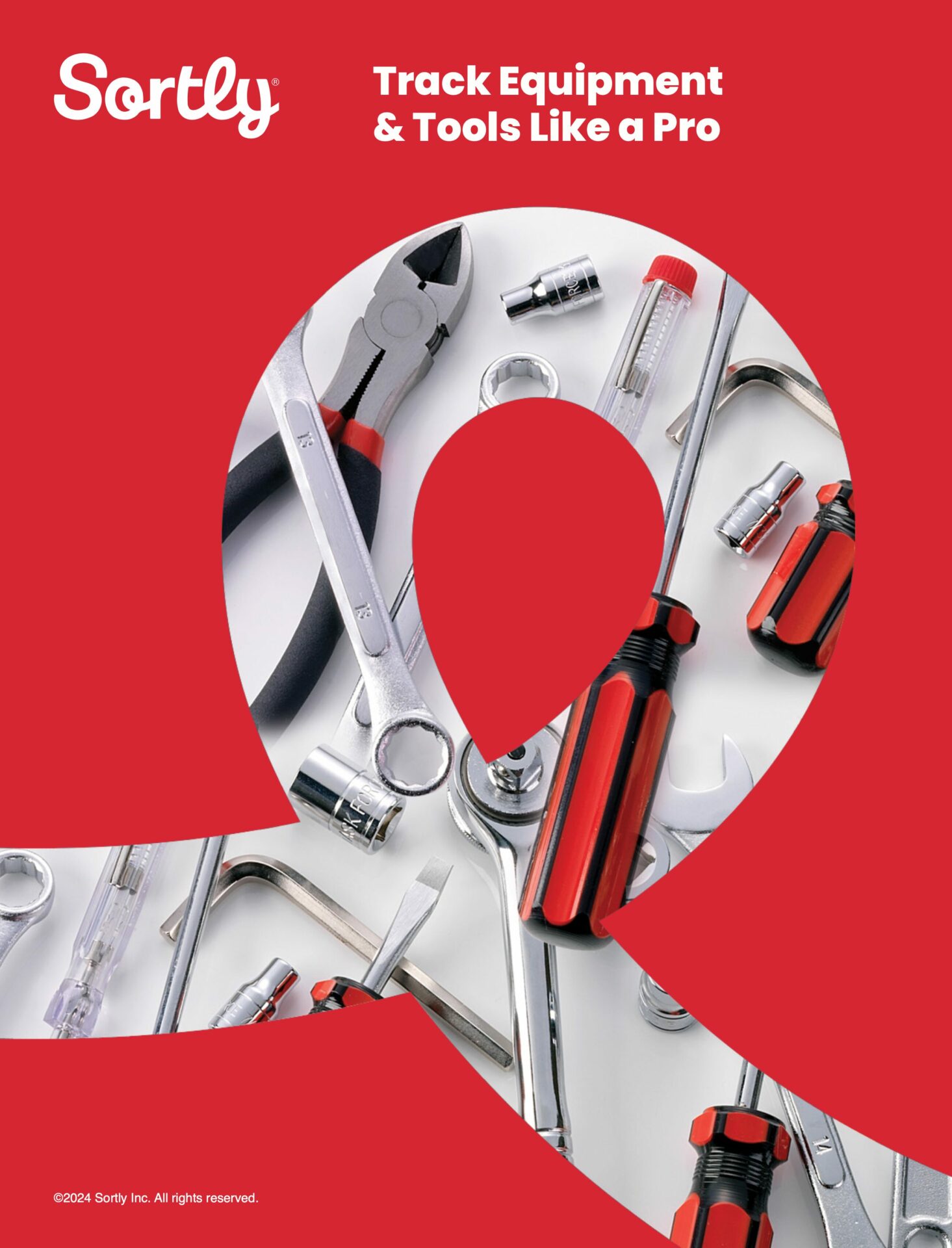
Free Ebook: Track Equipment & Tools Like a Pro
This easy, comprehensive guide can help you:
- Determine which details to track about your equipment and tools
- Set a standard operating procedure for asset tracking
- Perform physical audits of your business’s tools and equipment
2. Audit equipment from the onset
Regardless of what equipment management system you decide to utilize, it’s essential to audit equipment as soon as possible. As you set up your new equipment management system, categorize and digitize your inventory list. If you’re using a system like Sortly, it’s easy to add essential information to each item’s profile, including location details, item value, SKU, and more.
Consider creating custom fields and alerts to keep track of maintenance schedules, especially upcoming preventative maintenance and warranty end dates. Attach warranty documentation directly to each item so there’s no need to search a filing cabinet or your email if and when a problem arises.
If your team can’t audit all equipment at once, consider auditing by category or location over a fixed period until all equipment is accounted for. As you audit, reconsider how inventory is currently organized, and use this time to improve how inventory is stored and secured.
If you’re concerned about theft or storage conditions, consider implementing strategies to prevent inventory shrinkage or relocating inventory to more ideal conditions. This is especially true in fields such as construction, where equipment may rust or depreciate more quickly if not stored properly.
Related: How to Perform an Asset Audit
3. Consider barcodes and QR codes for fast perpetual inventory management
In equipment inventory management, perpetual inventory management refers to an inventory system where data is updated in real time. The only way to achieve perpetual inventory is to utilize inventory management software that enables instant checking in and checking out of equipment. To automate this process, generate barcodes and QR codes for all equipment your business maintains.
If you’re using Sortly, it’s easy to create custom barcodes and QR codes, and then prepare a unique label that can be printed and affixed to each piece of equipment. The barcode or QR code is automatically synced with each item’s profile, allowing your team to rapidly check equipment in and out as it is used, maintenance is performed, or the item is relocated.
Barcoding and QR-coding are great for high-value equipment that frequently changes hands and locations. Sortly customer Bilo Plumbing & Heating, for example, relies on QR codes for fast, precise inventorying. The Bilo team uses Sortly to generate a QR code for every piece of inventory, including equipment and tools. Then, it prints custom QR code labels that include the manufacturer’s name, the item description, and the part number.
4. Continue to optimize, train, and audit at least annually
Once your equipment inventory management system is up and running, you should periodically audit all of your equipment and improve processes as needed. Inventory audits should be performed at least once a year to confirm perpetual inventory records match physical inventory.
During this time, businesses can also assess depreciation, double-check maintenance schedules, update item profiles, and ensure current organizational and standard operating procedures remain ideal.
Optimize your equipment inventory management strategy with Sortly
If your business maintains more than a handful of equipment, keeping inventory records up-to-date may feel impossible. Sortly’s inventory management software helps streamline every aspect of an equipment inventory management system, from organizing and tracking inventory to generating key data and reports about those items.
Sortly enables all team members to manage inventory from any device, anywhere. We’re an intuitive inventory solution perfect for small businesses, especially those that stock equipment across multiple locations or employ team members who are always on the go. With Sortly, you can track equipment and anything else that matters to your business, including supplies, parts, tools, and other inventory and assets.
Learn more about how Sortly can help your business manage equipment inventory and get started with a free, two-week trial.